TABLE QUALITY INSPECTION
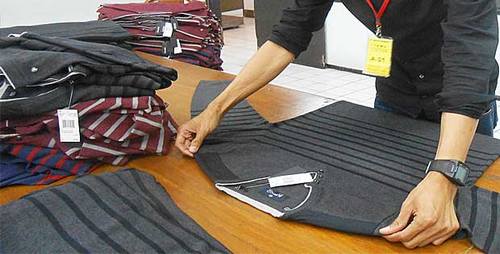
Table inspection:
After completion of production, each item is rigorously inspected on a table to locate any remaining defect. Item without defect is passed while defectives are rejected. Defectives are however, repaired if possible. Table inspection is the mainstream inspection method. It is also called “End of the line inspection system”. It is the most original inspection system the civilization has discovered in garment industry. Table inspection is done after the inline quality inspection.
Tools and environment requirement for table quality inspection:
The inspector who is trained must be equipped with the following tools and environment.
1. A wide table (of greenish grey color) lit with day light type of tube lights; light quantity should be enough to the tune of 1,000 flux.
2. A measuring tape; another measuring tape fixed on the table.
The inspector who is trained must be equipped with the following tools and environment.
1. A wide table (of greenish grey color) lit with day light type of tube lights; light quantity should be enough to the tune of 1,000 flux.
2. A measuring tape; another measuring tape fixed on the table.
3. Good quality scissors.
4. Required gummed paper arrow sticker to display location of defects etc.
5. Inspector must have a worksheet /P.O. sheet along with size spec.
6. Inspector must have special buyer instructions, if there is any.
7. For each style there should be an approved sample in close proximity to the inspector.
8. If your factory has a quality manual approved by buyer, check with major & minor defects as per that manual.
9. In absence of factory quality manual, should be use made of buyers manual where enlisting major & minor defects of garments.
Inspection procedure for table quality in the apparel industry:
There are some inspection procedures these are following to maintain for table quality inspection in the apparel industry.
- Keep your table and hands clean.
- Take the garments and put it spread on the table keeping the most important zone (Zone-A) in front of you.
- Locate any defect in this zone. If you identify any major defect, mark it and keep the garment in the Reject basket.
- If you identify the minor defects on the zone-A, mark them s major defects. Reject them and keep them in Major defect basket.
- Check zone-II & III or B & C of the garments and identify defects as per buyer’s instruction/ manual.
- Quality supervisor or Quality Manager will check major defect basket & Reject basket to check for repairable.
- Repairable garments will go to rework in a separate basket (Properly marked on the basket)
- They will be rigorously inspected separately.
- Garments remaining after sorting out of repairable garments from Reject basket & Major defect basket will be treated as rejects.
- Reject garments shall be kept in reject basket (Properly inscribed on the basket) and they will be under the full care of the quality manager until the shipment of the consignment.
- Garments passed by the inspectors shall be kept in baskets inscribed “Passed Garments”. They will flow on wards for lot pass.

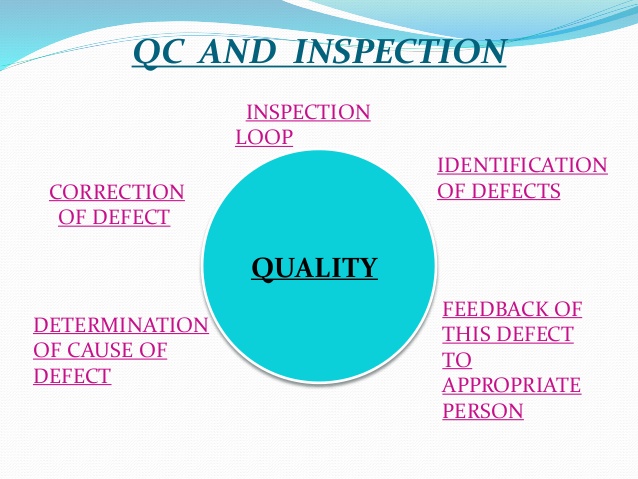